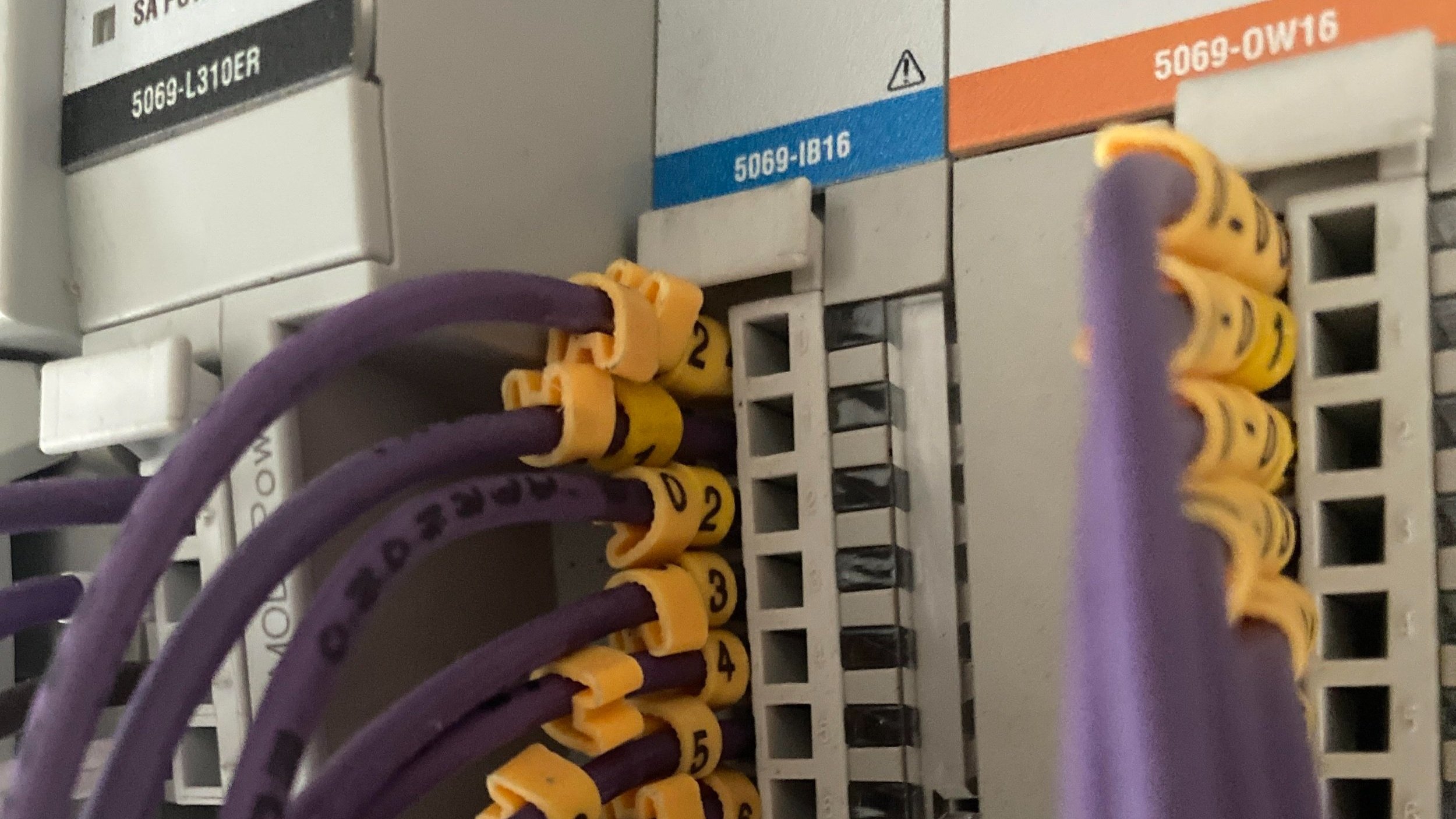
Frequently Asked Questions
FACTORY AUTOMATION FAQS
WHAT'S INVOLVED IN FACTORY AUTOMATION?
Factory automation involves the use of advanced technology, such as robots and computer system software, to increase efficiency and productivity in manufacturing processes. It can reduce the risk of errors from human operators and dramatically improve product consistency.
Factory automation can be used for tasks ranging from assembly line operations to packaging and shipping. For information about how we can provide cutting-edge automated processes for your business, simply get in touch with ACSE today.
WHAT ARE SOME EXAMPLES OF FACTORY AUTOMATION SYSTEMS?
Factory automation systems can range from simple, single tasks to incredibly complex operations.
One example might be a conveyor belt system, which helps to streamline the movement of materials within the factory. Other systems might involve robotic systems for fully automated tasks, such as packaging or assembly on a production line. Each of these aims to reduce the reliance on human factors and interference.
Some factories may even use completely automated machines for processes like welding or cutting. In addition to increasing efficiency and productivity, these systems have also improved employee safety by reducing the need for human workers to interact with potentially dangerous equipment.
WHAT ARE IIOT AUTOMATION ENGINEERING SERVICES?
Being a leading provider of automation engineering services, ACSE is also at the cutting edge of novel automating processes in Industry 4.0. This involves connecting mechanical processes on the factory floor to cloud technology, substantially improving the production system.
This industrial internet of things (IIoT) is the direction the business world is heading in, and we can help you prepare for it. In the long term, having smarter devices, more data, and more sophisticated robotic and technological processes will contribute immensely to the success of your business.
Whether you’re looking to improve your manufacturing process or simply rely less on human expertise, ACSE is here to help.
INDUSTRIAL AUTOMATION FAQS
WHICH COMPANIES OFFER INDUSTRIAL AUTOMATION NZ-WIDE?
If you’re looking for high-quality, reliable, and approachable industrial automation in NZ, look no further than ACSE Limited.
We provide leading warehouse and factory automation services for various industries, working with a collection of technologies such as SCADA, PLC Machine solutions, packaging robots and more.
If you want to increase productivity, automate your business and upgrade your workflows, get in touch with ACSE today.
WHAT’S INVOLVED WITH INDUSTRIAL AUTOMATION SOLUTIONS?
Industrial automation involves everything from software to hardware.
Software is a crucial aspect of any industrial automation process. This involves programming and problem-solving algorithms that control the actions of the hardware.
The hardware component includes machines and equipment that can carry out the automated processes coded with software.
Finally, there is the integration component, which involves connecting all elements in a cohesive system that allows for efficient and reliable operation.
WHICH INDUSTRIES CAN BENEFIT FROM INDUSTRIAL AUTOMATION?
The use of industrial automation technology can have a major impact on various industries.
Manufacturing, for example, can benefit from improved efficiency and consistency in production processes. Logistics and supply chain management can also see improvements through automated inventory tracking and transportation coordination.
Sectors such as Animal Health and agriculture have the potential to be transformed with the implementation of industrial automation systems. Industrial automation can help streamline efforts such as manual picking and packing.
WAREHOUSE AUTOMATION FAQ
WHAT IS WAREHOUSE AUTOMATION?
Warehouse automation refers to the use of technology and machinery to streamline the storage and distribution processes within a warehouse.
This can include the use of automated guided vehicles for material handling, robotic arms for picking and packing orders, and radio frequency identification (RFID) tags for inventory tracking.
Automated warehouse management systems can increase efficiency and productivity, reduce errors, and enhance safety for employees. This makes it a compelling and attractive proposition for most businesses, especially those working in the supply chain, manufacturing, packaging and processing industries.
HOW CAN I SAVE MONEY WITH AUTOMATED WAREHOUSE SYSTEMS?
Automated warehouse systems can significantly improve a company's profit margins.
For one, they can optimize storage space, allowing for more efficient use of the warehouse. This not only saves on the cost of expanding or renting additional space, but it can also cut down on overhead expenses such as electricity and labour costs.
Automated systems can also lead to increased accuracy and efficiency in picking, packing, and shipping orders, reducing errors and wasted time.
In addition, with warehouse automation systems, businesses can better track inventory levels and anticipate customer demands, leading to improved stocking decisions and decreased overstocking expenses.
WHAT ARE THE PRIMARY FEATURES OF WAREHOUSE AUTOMATION?
Warehouse automation technology involves everything from basic features to advanced solutions.
Basic automation might make use of scanning or printing procedures, which are relatively low-cost and low-maintenance.
The next level of integration might involve features like voice-directed technologies, automated guided vehicles, or automated storage and retrieval systems (AS/RS).
Finally, advanced automation might make use of solutions like automated sortation systems or autonomous mobile robots, which are more comprehensive in nature.
On a company level, this might look like an automated inventory management system which caters for end-to-end supply chain processes.
SCADA AUTOMATION FAQS
WHAT IS A SCADA CONTROL SYSTEM?
A SCADA control system, short for Supervisory Control and Data Acquisition, is a type of industrial control system that collects data from remote locations and allows for centralized control.
A supervisory system of this nature is used in a variety of industries. In energy management, for example, a SCADA system can monitor the status of power generation and distribution to ensure efficient operation.
The centralized nature of SCADA systems allows for real-time monitoring and control from a remote location, making them an essential tool in any industry.
HOW DOES A SCADA OPERATING SYSTEM WORK?
Supervisory control and data acquisition systems remotely monitor and control industrial equipment and processes.
Typically, the control equipment includes industrial machines, valves, and sensors. These are connected to the SCADA system through communication networks, such as Ethernet or radio waves, via an interface that uses a remote-control unit and programmable logic controller.
Together, this communication infrastructure provides inputs that will collect data, which is then used to inform decision-making.
Modern SCADA systems send signals to the equipment to start and stop certain processes, as well as gather data from sensors. This data can then be analyzed and used for decision-making and machine performance reports.
The SCADA system and radio modules work together to provide a combination of data acquisition, analysis, storage and reporting. In addition, radio SCADA systems allow operators to monitor and control system command functions from a remote location.
IS SCADA EQUIPMENT EXPENSIVE?
The cost of SCADA equipment can vary greatly depending on several factors, including the size and complexity of the system being implemented. These costs include not only the hardware and software but also technical expertise for installation and maintenance.
While the initial investment in a SCADA system may be high, it can often lead to long-term savings through improved efficiency and streamlined operations. Improved oversight provided by SCADA control systems can help prevent inefficiencies across your industrial processes, thanks to the collected data made available from its use.
PACKAGING ROBOTS FAQS
HOW DOES A ROBOT PACKAGING MACHINE WORK?
A robot packaging machine operates by automating the packaging process.
First, products enter the machine through a conveyor belt or other feeding system. The robot then picks up the item with its arm and places it into a package or container.
The package is sealed and labelled before being placed onto another conveyor belt for shipment. This process can be highly customisable and can package a wide variety of items with speed and precision.
In addition, robotic packaging machines often boast advanced safety features to ensure the safety of both the products and human workers.
WHAT ARE THE BENEFITS OF AN OMRON ROBOT FOR PACKAGING?
The OMRON offers a range of benefits for packaging robot operations, no matter what your production needs may be.
Its advanced vision and gripping technology allow for precise handling of products, from small items to large bags or boxes. You might require case packing, carton loaders, or another set of packaging systems entirely. These capabilities can offer a huge boost to those working in the food industry.
The robot's flexibility also means it can easily adapt to changing tasks and product sizes, increasing efficiency and minimizing downtime. This makes our automated packaging solutions
If you are looking to implement an OMRON packaging robot system in your factory or warehouse, contact ACSE today for an initial consultation.
WHAT IS THE DIFFERENCE BETWEEN COLLABORATIVE - COBOT ROBOTS AND UNIVERSAL ROBOTS?
When it comes to industrial robots, the terms collaborative - cobot and universal are often used interchangeably. However, they do refer to two distinct types of robots.
A universal robot can perform a wide variety of tasks and can adapt to changing environments or processes.
On the other hand, a collaborative - cobot robot is designed to work alongside human workers in shared workspaces without the need for extensive safety measures such as cages or barriers.
MACHINE VISION SYSTEMS FAQS
WHAT ARE INDUSTRIAL VISION SYSTEMS?
Industrial vision systems are computer-controlled cameras used in manufacturing and production processes. They allow for automatic inspection, identification, and measurement of products, helping to ensure quality control and improve efficiency.
These industrial cameras can also be used for robotics guidance, error-proofing, and tracking of materials.
HOW DO MACHINE VISION SYSTEMS WORK?
The right vision system will make use of cutting-edge technology to interpret a digital image. This includes the use of ambient light rays at a particular working distance, focal length, and resolution to ensure quality every time.
This technology allows vision systems, like line scan cameras, to perform appearance inspections and other tasks.
WHAT DOES A VISION SYSTEM CAMERA DO?
A vision system camera is a type of machine vision technology that uses a camera to capture visual information and analyze it for various purposes.
Machine vision cameras can be used in industrial settings for quality control and robotic guidance. They can also be used in medical and scientific research, surveillance, and autonomous vehicles.
Vision system cameras have advanced capabilities such as pattern recognition and object detection, making them valuable tools for a variety of industries and applications. Machine vision systems are used on production lines for product inspection and character recognition.
PLC MACHINE FAQS
HOW DOES A PLC CONTROLLER WORK?
A programmable logic controller, or PLC controller, is an essential tool in automation and manufacturing. It uses a program to automate various processes and tasks, often replacing the need for manual labour.
Programmable logic controllers are input and output devices, meaning each component receives inputs and regulates outputs. This takes place with various programming languages via a central processing unit (CPU).
Input devices such as sensors send signals to the controller about the current state of the system. The PLC then uses its graphical programming language to process this information and make decisions about what actions need to be taken.
Output devices, such as motors or valves, are activated based on these decisions. By constantly monitoring inputs and adjusting outputs, the programmable controllers can automate a wide range of processes efficiently and accurately.
HOW DOES A PLC MACHINE INTERACT WITH DATA?
A PLC Machine’s inputs will come from a range of data points, either from manual entry or from a pre-programmed database. This data will inform the PLC system whether it should change its output or not. PLC systems also make extensive use of ladder logic and function block diagram methods, to interpret incoming and outgoing data.
WHAT ARE THE BENEFITS OF A PLC MACHINE?
Easily programmable, relatively affordable, and highly versatile, PLCs can offer a great deal to a variety of business processes. With no moving parts, they are reliable and can be trusted to perform consistently in industrial settings. When technical problems do arise, PLCs are easy to fix, and in general, they do not consume very much power.